人浏览过该文章
用于特殊工况的镍基合金材料系列 (二)
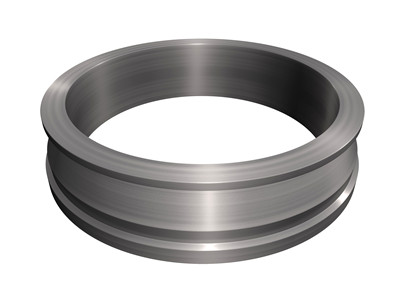
用于特殊工况的镍基合金材料系列 (二)
在昨天发布的用于特殊工况的镍基合金材料系列 (一)一文中,我们分析了针对还原性酸介质选择耐腐蚀材料的一些重要考虑因素,并得出了两点结论:
一般来说,除氢离子外的氧化剂越多,就需要越高的铬含量。这是选材的第一个基本原则;钼与铬的结合对耐点蚀和缝隙腐蚀性能有非常重要的影响,铬含量和大约3.3倍的钼含量之和(即所谓的耐点蚀当量)至关重要,这是选材的另一个基本原则。
在本篇文章中,我们会借助几张图表继续分析针对还原性酸介质选材的考虑因素。
铜有利于合金材料在还原性介质硫酸中钝化,从而减少腐蚀。这可能是由于腐蚀处会形成铜层,有一定的保护作用。因此,铜在20世纪80年代之前曾被广泛看作耐腐蚀材料的合金元素之一。但随着技术发展,人们认识到,合金中添加较高铜含量不利于在含氯元素的水介质中的耐缝隙腐蚀性能。因此,后来开发的材料中铜的添加量一般不高于2%。如今普遍都低于1%。
此外,随着镍含量的增加,不仅奥氏体对铬和钼的溶解度增加,而且耐蚀性普遍有所增强。因为镍降低了活性状态下的腐蚀速率并且促进了钝化产生,镍含量对于不锈钢铁铬合金耐酸腐蚀性能有很大影响。因此合金的耐酸腐蚀性能随镍含量增加而提高是选材的另一个基本原则。然而,由于一些具体细节原因,这一原则可能会出现一些偏差。因为其他合金成分,特别是之前提到的铬、钼和铜元素,也会对耐腐蚀性产生共同影响。
合金的耐酸腐蚀性能一般与镍含量成正比这一选材的基本原则,也适用于抗氯化物引起的应力腐蚀开裂。
(图1:奥氏体钢在静态中等浓度硫酸中添加Fe3+作为氧化剂的耐腐蚀性范围,以Fe2(SO4)3形式添加,共试用3个试样,测试超过7天)
两个例子的目的是为了说明材料与硫酸之间的相互作用,如果材料选择得当,就能获得理想的耐腐蚀性能。图1显示了特种不锈钢 Alloy 33(1.4591)在中浓度硫酸中的耐受范围如何随着硫酸中氧化性Fe3+离子含量增加, H2SO4浓度增大以及温度升高而扩大。由于铬的含量非常高,这种材料不仅适合用于处理多种氧化性介质,而且它需要这类介质才能实现耐腐蚀性能。另一方面,图2显示,即使只是在硫酸中存在少量的氧化性成分,例如溶解的空气中的氧气,也足以使Alloy 31(1.4562)在整个硫酸浓度范围内具有相对较高的耐腐蚀性,这也是这种材料中高铬和高钼含量相结合的结果。
对于磷酸的处理,根据使用条件,也可以选择表1所示的材料。磷酸工业的典型材料是Alloy 904 L (1.4539),但 Alloy 31 (1.4562)已被证明非常适合磷酸生产中遇到的腐蚀性工况。因此,在选择处理磷酸材料时,尤其是腐蚀性特别高的工作条件下时,基本原则是选择铬含量高,同时含钼的材料。
对于工业生产中第三种重要的还原性酸——盐酸,表1中只有少数材料可以使用。对于较高的酸浓度和温度范围,首先考虑表1中的 Alloy N10675。
但是,随着盐酸在大气中暴露程度和氧化性物质的增加,镍-钼合金的适用性表现出明显的局限性。
镍-铬-钼合金在特定条件下也适用于处理盐酸。根据图3所示的腐蚀图,只要室温下HCl浓度不超过8%,就可以使用 Alloy 31(1.4562)。因此, Alloy 31以及以其为基础开发的Alloy 31 Plus(2.4692)可被考虑用于在化学反应过程中形成少量盐酸的应用。在镍-铬-钼材料中, Alloy 59 (2.4605)具有非常出色的耐腐蚀性。
在图4所示的腐蚀图中可以看见0.13mm/年的腐蚀速率曲线,在 40℃以上、浓度至40%的HCl中都超出了耐腐蚀性材料的标准。但材料的耐腐蚀范围会因盐酸的暴露在空气中的程度和其他氧化性物质的存在而改变,因此图3和图4只是提供一个参考。
Alloy 2120 MoN可用于许多化学工艺的还原性和氧化性介质中。高含量的铬和钼使该合金具有很强的抗氯离子侵蚀能力。Alloy 2120 MoN的耐点蚀当量PREN值为86(PREN=%Cr+3.3Mo+30N)。总的来说,该材料在耐缝隙腐蚀和点蚀方面优于其他C合金。另外,它还在盐酸、硫酸等还原性酸中表现出卓越的耐腐蚀性。此外,按照ASTM G28测试A法, Alloy 2120 MoN表现出良好的抗晶间腐蚀能力。
有机酸也属于还原性酸。表1中列出的材料可作为备选材料,但实际情况下需要考虑有机酸中包含的其它成分以及其它运行条件。
在下篇文章中,我们会继续介绍耐氧化酸腐蚀的材料,并展示更多的材料数据,敬请期待!